Buckner HeavyLift Cranes: Ballast Trays vs. Ballast Wagons
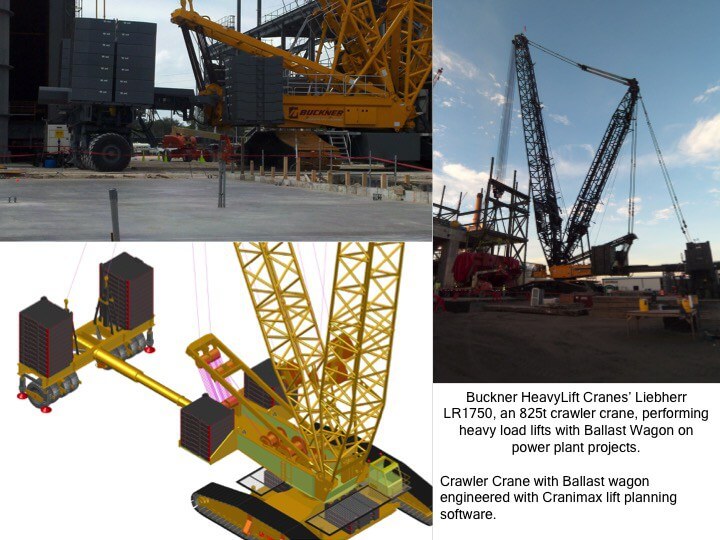
Buckner HeavyLift Cranes: Ballast Trays vs. Ballast Wagons
When utilizing a Liebherr lattice boom crawler crane on a heavy lift project, planning considerations go far beyond just the lifting radius and load capacity chart. The true strength of lattice boom crawler cranes comes from the utilization of additional heavy lift ballast in forms of a tray or wagon, sometimes also referred to as “bogey,” “buggy,” “maxer,” or “superlift.” Both trays and wagons significantly increase the crawler crane’s lifting capacities; however, there are differences to consider when lift planning for your specific job.
Using a wagon (“BW”) rather than a tray (“B”) offers the primary advantage of ease of use in high volume, repetitive work. A wagon can be loaded to its maximum capacity and still allow the crane to swing, even with no load on the hook, increasing the flexibility of lifting operations and simplifying preliminary planning. When there is no need to “float” the wagon to specific locations, as would be done with a tray, small deviations in pick and set locations are less of an issue.
The flexibility of a wagon is not without added complexity as site preparation required to utilize a wagon can be extensive, due to the large weights involved. For example, Buckner’s Liebherr LR 11000 wagon can handle up to 992,000lbs of counterweight. This large amount of counterweight can still be moved as the crane slews with no load on the hook, but the wheels will travel along the matted surface the crane rests on. If the wheels are orientated for slewing, it is possible for the entire weight of the wagon to rest only on two or three mats, leading to massive ground bearing pressures. As a compromise, it is common in the heavy lift industry to build a “dance floor” comprised of two layers of mats, stacked perpendicular to one another ensuring the load will still be spread over a larger area, due to the perpendicular second layer, in the case the wagon wheels do end up isolated on only a few mats. One major advantage of the wagon on Liebherr crawler cranes is the ability to scope in and out during operation, changing the radius. This can be useful for avoiding obstacles, but changes the capacity of the crane, and thus requires precise planning.
One example of the wagon helping with high volume work was a Buckner Liebherr LR1400, a 440t crawler crane, erecting steel at Texas A&M. The wagon was required for the long boom and luffer combination, reaching far into the stadium with heavy trusses. The flexibility of the wagon allowed the crane to carry full counterweight between lifts and still be able to slew as normal.
In contrast to using a wagon, the heavy lift tray has advantages in major, non-repetitive lifts. The need to “float” the tray during the lift allowing the crane to slew requires more precise planning in advance, but offers less preparation work in the field. Rather than a massive “dance floor,” matting is only required at the locations where the tray will be set on the ground. The tray does however require a more precise amount of counterweight in order to properly float during a lift. It is generally not possible to float a loaded tray without a substantial load on the hook, so counterweight may need to be removed before and/or after a heavy lift. On Liebherr crawler cranes, the radius of the tray is controlled by the angle of the derrick, so it is also possible to vary this radius during lifting activities.
The main difference between changing the radius of a tray versus a wagon is that while the capacity will still change with the tray, it also changes the allowable range of counterweight to float the tray. This again requires precise planning to prevent a situation where the tray rests on the ground when it is not desired.
One additional configuration option with Liebherr crawler cranes is the “B2” tray, which is essentially the standard tray, but with an additional lattice strut to push the tray further back than the derrick would normally allow. The downside is that this requires a specific, fixed radius that cannot be changed during lifting. As an example, Buckner’s Liebherr LR 11000 can operate with a B2 tray at 20m, 25m, or 30m. This mode is most useful when tailswing obstructions are not an issue.
Another benefit is that the B2 configuration can actually increase capacity at radii that the normal B tray could achieve on its own. The reason for this is the angle of the derrick. When a crane is operating with a standard B tray, the tip of the derrick is directly above the center of the tray. In B2 mode the derrick will sit at a much closer radius, 12m for the LR 11000 as an example. This change in the derrick angle, relative to the main boom, often leads to an increase in capacity, most noticeable at a high main boom angle.
While ballast trays may require more precise planning, they do offer the convenience of having less site preparation, while adding significant increases to lifting capacities. Ballast wagons can provide flexibility in increasing heavy lifting capacities, allowing ease of use in repetitive lifting operations. Both trays and wagons provide solutions to heavy lifting needs in high volume jobs. Buckner HeavyLift Cranes offers in house lift planning that is essential when making crucial decisions on your heavy lift job. Buckner’s lift planner will be able to accurately assess the specific job, job site, and needs in order to safely perform a heavy lift. This is just one of the many services offered to Buckner HeavyLift Cranes’ partners.
Be sure to call Nick Leveski at Buckner HeavyLift Cranes for more information on assistance in planning your upcoming crawler crane needs at: 336.213.9034.
Learn more about Buckner HeavyLift Cranes’ Lift Planning Services on our Engineered Lift Planning page.